From Shop Floor to C-Suite: How Metal Fabrication Companies Are Forging Leadership Talent
Companies
2025-02-17 12:00:00Content
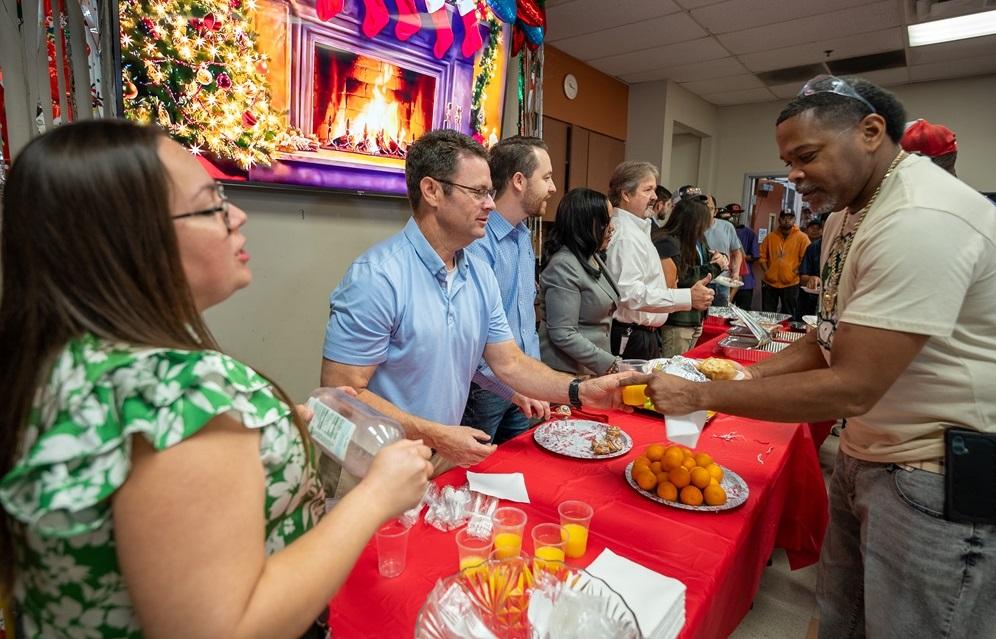
Special Products and Manufacturing: A Success Story of Growth and Skill Development
In the dynamic world of manufacturing, success is often measured by the ability to adapt, innovate, and invest in human potential. Special Products and Manufacturing (SPM) stands as a shining example of this principle, demonstrating how nurturing employee skills can directly translate to business expansion and excellence.
The company's remarkable journey has not gone unnoticed. In recognition of their outstanding achievements, SPM has been honored with The Fabricator's 2025 Industry Award, a prestigious acknowledgment of their commitment to professional development and operational excellence.
At the heart of SPM's success is a strategic approach to employee growth. By providing continuous training, supporting skill enhancement, and creating a culture of learning, the company has transformed its workforce into a powerful engine of innovation and productivity.
As employees have expanded their capabilities and expertise, SPM has simultaneously witnessed significant business growth. This symbiotic relationship between individual skill development and organizational progress has positioned the company as a leader in the manufacturing sector.
The 2025 Industry Award is more than just a trophy—it's a testament to SPM's forward-thinking approach and their understanding that investing in people is the most crucial investment a company can make.
Forging Success: How Skill Development Transforms Metal Fabrication Enterprises
In the dynamic world of metal fabrication, success is not merely about machinery and equipment, but about the human capital that drives innovation and growth. This article explores the remarkable journey of a company that has transformed its business landscape through strategic skill development and employee empowerment.Unlocking Potential: The Catalyst of Organizational Transformation
The Evolution of Workforce Capabilities
Metal fabrication is an intricate industry where technological prowess meets human expertise. Special Products and Manufacturing represents a compelling case study of how intentional skill enhancement can revolutionize an organization's trajectory. By investing systematically in employee development, the company has not just improved individual competencies but fundamentally reshaped its competitive positioning in the market. The organization's leadership recognized early that technical skills are the cornerstone of manufacturing excellence. They implemented comprehensive training programs that went beyond traditional technical instruction, focusing on holistic professional growth. These initiatives encompassed advanced technical training, soft skills development, problem-solving workshops, and cross-functional learning opportunities.Strategic Learning Ecosystem
Creating a robust learning ecosystem requires more than sporadic training sessions. Special Products and Manufacturing developed a sophisticated approach that integrated continuous learning into its organizational DNA. They established mentorship programs where experienced professionals guided emerging talents, creating a knowledge transfer mechanism that preserved institutional wisdom while nurturing innovation. Technology played a crucial role in this transformation. The company leveraged digital learning platforms, virtual reality simulations, and interactive training modules that allowed employees to acquire skills in immersive, engaging environments. These technological interventions made learning more accessible, personalized, and aligned with individual learning preferences.Cultural Transformation through Skill Development
Beyond technical competencies, the organization cultivated a culture of continuous improvement and intellectual curiosity. Employees were encouraged to challenge existing processes, propose innovative solutions, and view learning as a lifelong journey rather than a one-time event. This cultural shift created an environment where professional growth was not just supported but celebrated. Performance metrics reflected the profound impact of these initiatives. Employee engagement scores increased, turnover rates declined, and the company witnessed a remarkable surge in operational efficiency. The correlation between skill development and business performance became increasingly evident, validating the strategic investments in human capital.Technological Integration and Skill Adaptation
As technological landscapes in metal fabrication evolved rapidly, the company remained agile. They developed adaptive learning frameworks that allowed employees to quickly assimilate emerging technologies like advanced robotics, AI-driven manufacturing processes, and sophisticated computer-aided design tools. This proactive approach ensured that their workforce remained at the cutting edge of industry innovations. The ripple effects of these comprehensive skill development strategies extended beyond internal operations. Clients and industry partners began recognizing the company as a benchmark for professional excellence, attracting high-value projects and establishing a reputation for delivering superior quality and innovative solutions.Future-Proofing through Continuous Learning
Special Products and Manufacturing's journey illustrates a fundamental truth: in modern manufacturing, human potential is the most critical competitive advantage. By creating a learning-centric environment that values individual growth, technological adaptation, and collaborative innovation, organizations can transform challenges into opportunities. Their approach serves as an inspirational model for businesses seeking to navigate the complex, rapidly changing landscape of modern manufacturing. It demonstrates that strategic investment in human capital is not an expense but a powerful catalyst for sustainable growth and industry leadership.RELATED NEWS
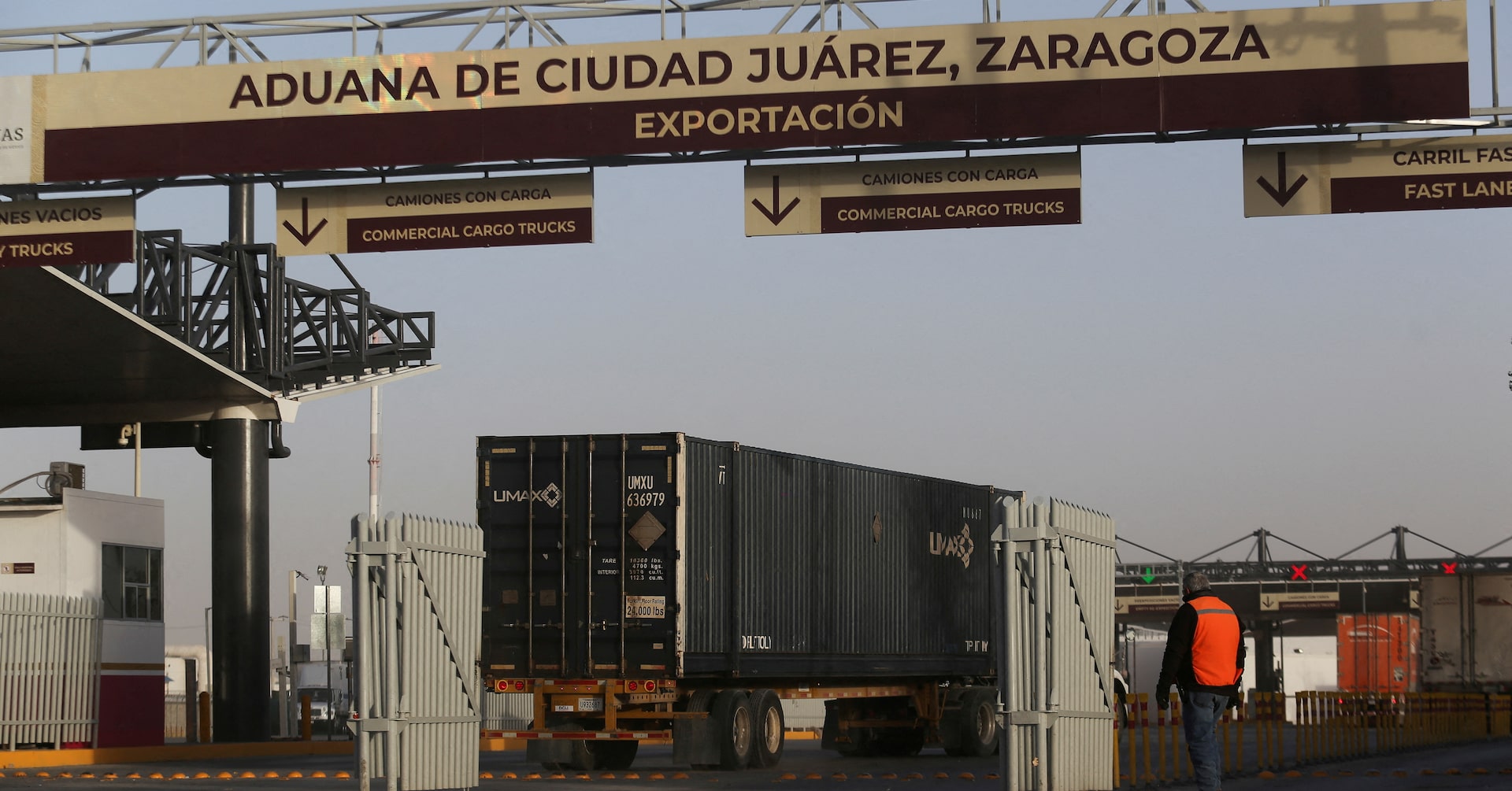
Trade Tension Tactics: Mexican Exporters Pause Shipments, Betting on Tariff Reprieve
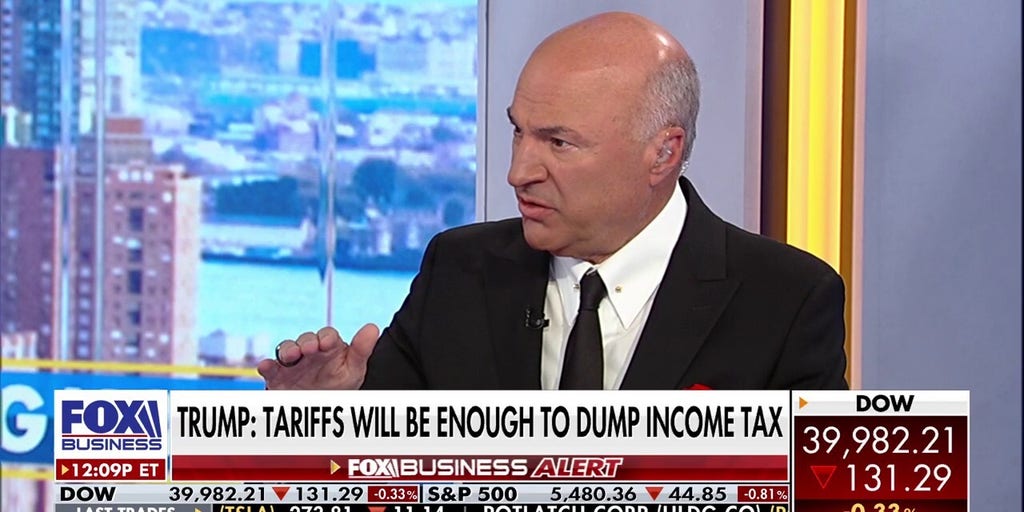
Wall Street Shakeup: O'Leary Warns of Potential Mass Exodus of Chinese Stocks from US Markets
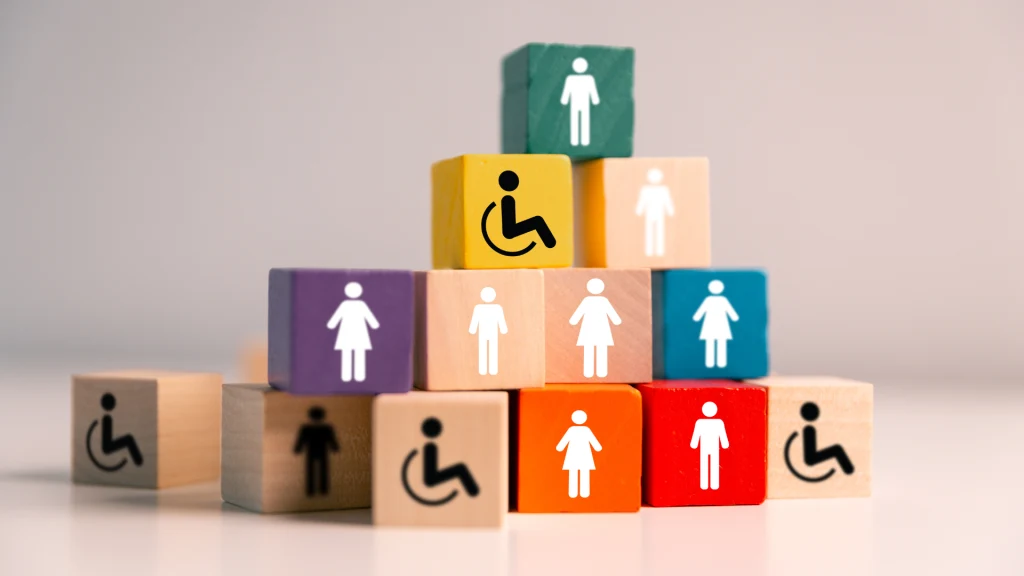