Trade Tremors: Companies Scramble to Reroute Global Supply Chains Amid Trump Tariff Tsunami
Business
2025-02-21 00:03:23Content
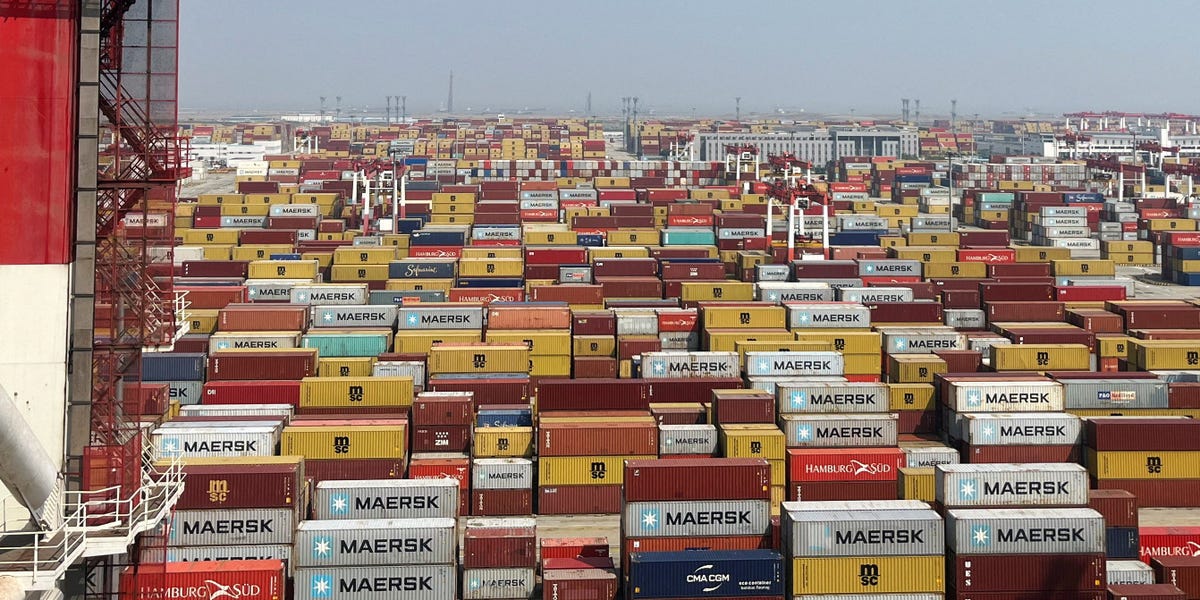
As trade tensions between the United States and China continue to escalate, businesses are facing a critical crossroads in their supply chain strategies. The Trump administration's aggressive tariff policies have sent shockwaves through global commerce, prompting companies to reevaluate their manufacturing and sourcing approaches.
Caught in the crossfire of an increasingly complex economic landscape, entrepreneurs and corporate leaders are now wrestling with a pivotal question: Is it time to diversify and relocate their supply chains away from China? The financial implications are significant, with potential cost increases, operational disruptions, and strategic realignments looming on the horizon.
Many businesses are exploring alternative manufacturing destinations, considering countries like Vietnam, Mexico, and India as potential replacements for their Chinese production networks. The tariff-induced uncertainty has transformed what was once a stable global supply chain into a dynamic and unpredictable environment, forcing companies to become more agile and strategic in their international business planning.
While the challenges are substantial, forward-thinking organizations view this disruption as an opportunity to reimagine their global sourcing strategies, potentially creating more resilient and adaptable supply chains for the future.
Global Supply Chain Reshuffling: How Trump-Era Tariffs Sparked a Corporate Exodus from China
In the complex landscape of international trade, businesses have been forced to confront unprecedented challenges as geopolitical tensions and economic policies reshape global manufacturing strategies. The implementation of tariffs during the Trump administration created a seismic shift in how companies approach their international supply chain operations, triggering a massive reevaluation of long-established manufacturing relationships.Navigating Economic Uncertainty: The High-Stakes Game of Global Manufacturing
The Tariff Tremors: Understanding Economic Disruption
The economic landscape transformed dramatically as businesses confronted the unprecedented challenges posed by targeted tariffs. Multinational corporations found themselves at a critical crossroads, forced to make strategic decisions that would fundamentally alter their operational frameworks. The punitive tariffs imposed on Chinese imports created a domino effect, compelling companies to explore alternative manufacturing destinations and reassess their global sourcing strategies. Companies discovered that maintaining existing supply chains had become exponentially more complex and financially burdensome. The additional costs introduced by tariffs eroded profit margins and necessitated innovative approaches to international manufacturing. Executives were compelled to conduct comprehensive cost-benefit analyses, weighing the potential risks and opportunities presented by potential geographic relocations.Strategic Relocation: Emerging Manufacturing Alternatives
As businesses sought to mitigate the financial impact of tariffs, several emerging markets presented compelling alternatives to traditional Chinese manufacturing. Southeast Asian nations like Vietnam, Thailand, and Malaysia emerged as attractive destinations, offering competitive labor costs and increasingly sophisticated manufacturing infrastructures. The geopolitical reconfiguration went beyond mere economic calculations. Companies began implementing sophisticated risk management strategies, diversifying their manufacturing bases to reduce vulnerability to potential future trade disruptions. This approach represented a fundamental reimagining of global supply chain architectures, moving away from concentrated dependency on a single geographic region.Technological Adaptation and Supply Chain Resilience
The tariff-induced transformation accelerated technological innovation within supply chain management. Companies invested heavily in digital technologies, blockchain tracking systems, and advanced predictive analytics to enhance operational flexibility. These technological interventions allowed businesses to create more responsive and adaptable manufacturing ecosystems. Advanced data analytics enabled companies to model complex scenarios, predicting potential disruptions and developing contingency strategies. The integration of artificial intelligence and machine learning technologies provided unprecedented insights into supply chain dynamics, allowing for more nuanced and strategic decision-making processes.Economic and Geopolitical Implications
The broader economic implications of this supply chain restructuring extended far beyond individual corporate strategies. National economies experienced significant shifts, with some emerging markets experiencing rapid industrialization while others faced potential economic marginalization. The reconfiguration represented a complex global economic realignment, challenging traditional notions of international trade and manufacturing. Governments worldwide began developing more proactive industrial policies, recognizing the strategic importance of maintaining robust and flexible manufacturing capabilities. The experience highlighted the intricate connections between trade policy, technological innovation, and economic competitiveness.Future Outlook: Continuous Adaptation
The lessons learned during this period of economic transformation suggested that flexibility and strategic foresight would be crucial for future business success. Companies that demonstrated agility, technological sophistication, and a willingness to challenge traditional manufacturing paradigms were most likely to thrive in an increasingly complex global economic environment. The tariff-induced supply chain revolution represented more than a temporary economic adjustment—it signaled a fundamental restructuring of global manufacturing strategies, driven by geopolitical tensions, technological innovation, and the relentless pursuit of operational efficiency.RELATED NEWS
Business
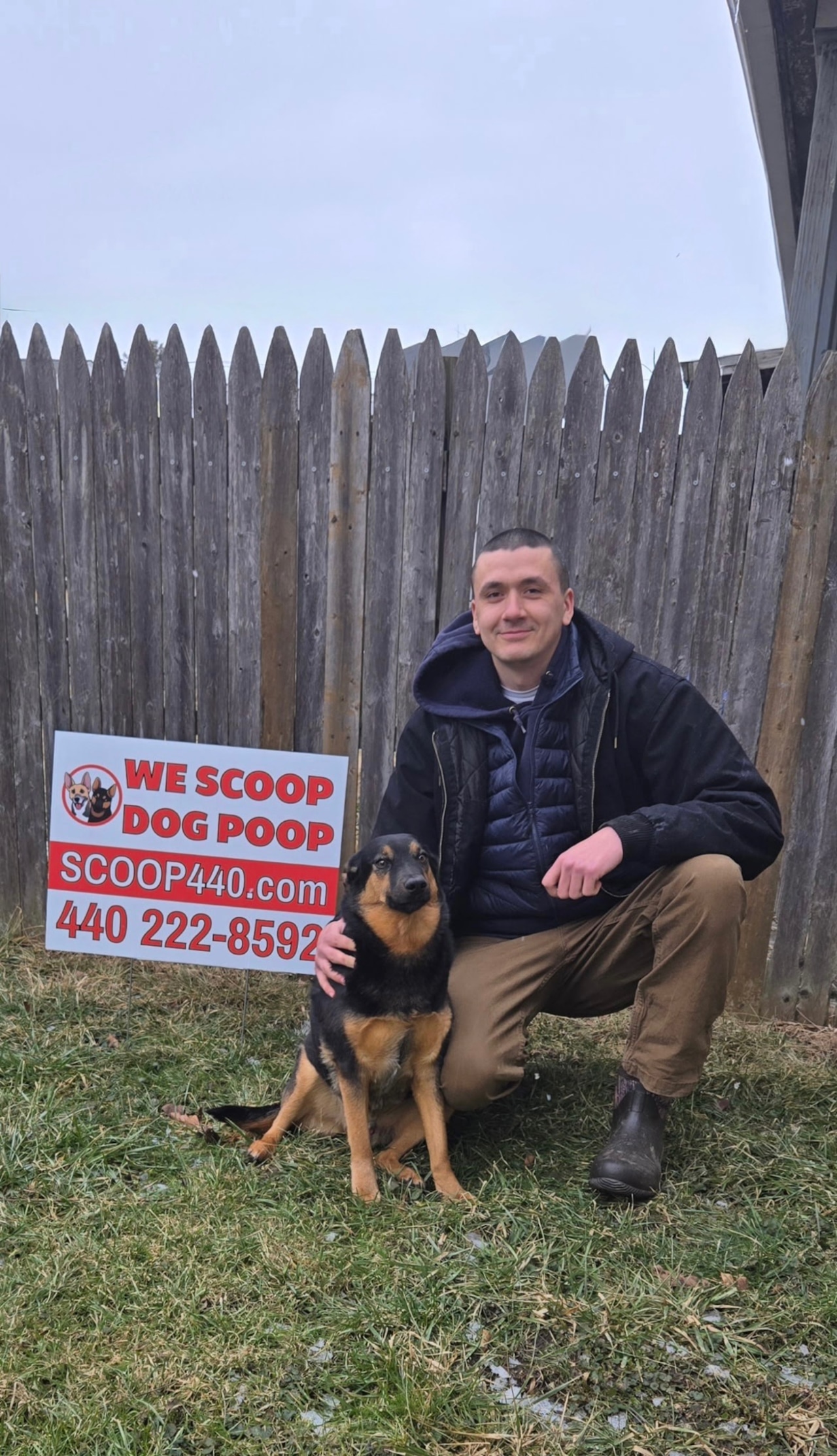
Local Prodigy Tops the Throne in Waste Management: Avon Lake's Unlikely Success Story
2025-02-19 13:40:44