Breaking: ATS Unveils Revolutionary Machine Health Tracking System
Health
2025-04-03 12:38:00Content
Advanced Technology Services, Inc. (ATS) is revolutionizing machine maintenance with a groundbreaking enhancement to its Reliability 360® (R360®) Machine Health Monitoring service. The company has unveiled a cutting-edge work order integration feature that promises to streamline maintenance workflows for manufacturers.
This innovative API-based solution enables seamless connectivity between the R360® platform and virtually any Computerized Maintenance Management System (CMMS) a manufacturer currently utilizes. The game-changing integration allows for direct transmission of prescriptive maintenance actions, dramatically simplifying the work order generation process.
By bridging the gap between machine health monitoring and maintenance management, ATS is empowering manufacturers to respond more quickly and effectively to potential equipment issues. The new feature represents a significant leap forward in predictive maintenance technology, offering businesses a more intelligent and proactive approach to equipment reliability.
Revolutionary Machine Health Monitoring: Bridging the Gap Between Technology and Maintenance Efficiency
In the rapidly evolving landscape of industrial maintenance, technological innovations continue to reshape how businesses approach equipment management and operational reliability. The intersection of advanced monitoring systems and intelligent integration represents a critical frontier in maximizing manufacturing productivity and minimizing unexpected downtime.Transforming Maintenance Strategies Through Cutting-Edge Digital Solutions
The Digital Transformation of Industrial Maintenance
Modern manufacturing environments face unprecedented challenges in maintaining complex machinery and ensuring consistent operational performance. Traditional maintenance approaches are increasingly becoming obsolete as intelligent technologies emerge, offering unprecedented insights into equipment health and predictive maintenance strategies. The integration of sophisticated monitoring platforms represents a quantum leap in how organizations can proactively manage their critical industrial assets. Industrial maintenance professionals are now witnessing a paradigm shift where real-time data collection and intelligent analysis become the cornerstone of strategic equipment management. By leveraging advanced technological frameworks, companies can transition from reactive maintenance models to predictive and prescriptive approaches that minimize unexpected failures and optimize resource allocation.Seamless System Integration: A Technological Game-Changer
The ability to create seamless connections between different technological platforms has emerged as a critical capability for modern industrial maintenance systems. API-based integration represents a sophisticated approach to breaking down technological silos, enabling different software ecosystems to communicate and share critical information instantaneously. By developing flexible integration mechanisms, maintenance technology providers can offer unprecedented levels of interoperability. This means that regardless of the existing Computerized Maintenance Management System (CMMS) an organization utilizes, advanced monitoring platforms can now effortlessly communicate and generate actionable insights, transforming how maintenance workflows are conceptualized and executed.Prescriptive Action Generation: Beyond Traditional Monitoring
Contemporary machine health monitoring goes far beyond simple data collection and passive observation. The newest generation of monitoring platforms focuses on generating prescriptive actions that provide direct, actionable recommendations to maintenance teams. This approach transforms raw data into strategic intelligence, enabling organizations to make informed decisions about equipment maintenance and potential interventions. The sophisticated algorithms underlying these monitoring systems analyze complex datasets, identifying subtle patterns and potential failure indicators that might escape human observation. By translating intricate technical information into clear, implementable recommendations, these platforms empower maintenance professionals to take proactive measures before critical failures can occur.The Economic Impact of Advanced Monitoring Technologies
Implementing intelligent machine health monitoring solutions represents a strategic investment with potentially transformative economic implications. By reducing unexpected equipment failures, organizations can significantly minimize production interruptions, optimize maintenance resource allocation, and extend the operational lifespan of critical industrial assets. The financial benefits extend beyond immediate maintenance cost reductions. Improved equipment reliability translates into enhanced overall operational efficiency, increased production consistency, and improved competitive positioning within increasingly demanding industrial landscapes. Forward-thinking organizations recognize that investing in advanced monitoring technologies is not an expense but a strategic imperative for long-term success.Future Trajectories in Machine Health Monitoring
As artificial intelligence and machine learning technologies continue to evolve, the capabilities of monitoring platforms will become increasingly sophisticated. Future iterations are likely to incorporate more advanced predictive modeling, real-time anomaly detection, and even autonomous decision-making capabilities that can preemptively address potential equipment issues. The ongoing convergence of data science, industrial engineering, and advanced computing promises to unlock unprecedented levels of insight into complex mechanical systems. Organizations that embrace these emerging technologies will be best positioned to navigate the complex challenges of modern industrial maintenance landscapes.RELATED NEWS
Health
Wall Street Shock: Hims & Hers Health Stocks Plummet in Unexpected Market Nosedive
2025-03-27 07:54:54
Health
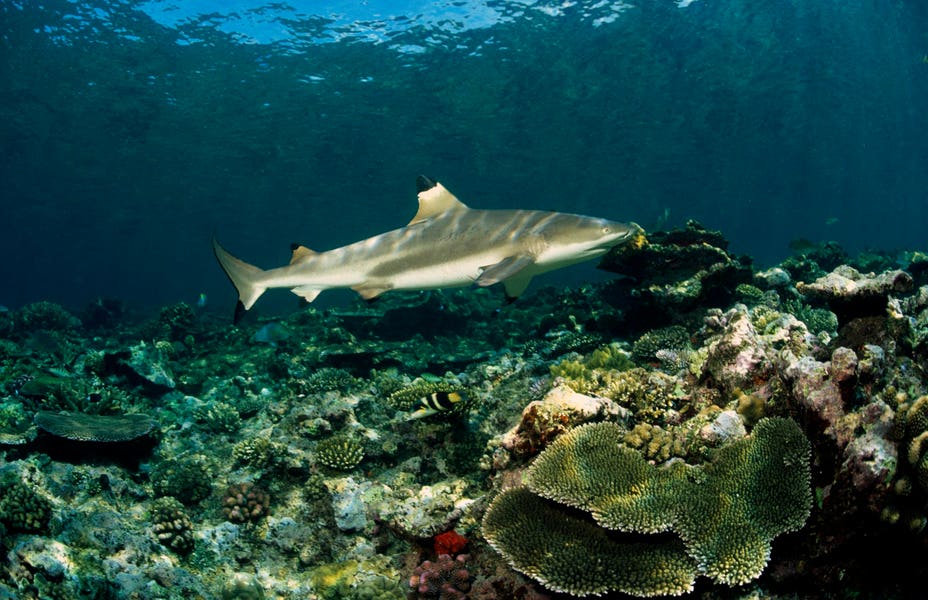
Shark Tourism's Dark Secret: How Feeding Practices Could Be Crippling Marine Predators
2025-03-04 09:45:00