The Quest for Perfect Discs: Inside the Tech Race to Solve Manufacturing Consistency
Companies
2025-02-19 19:53:52Content
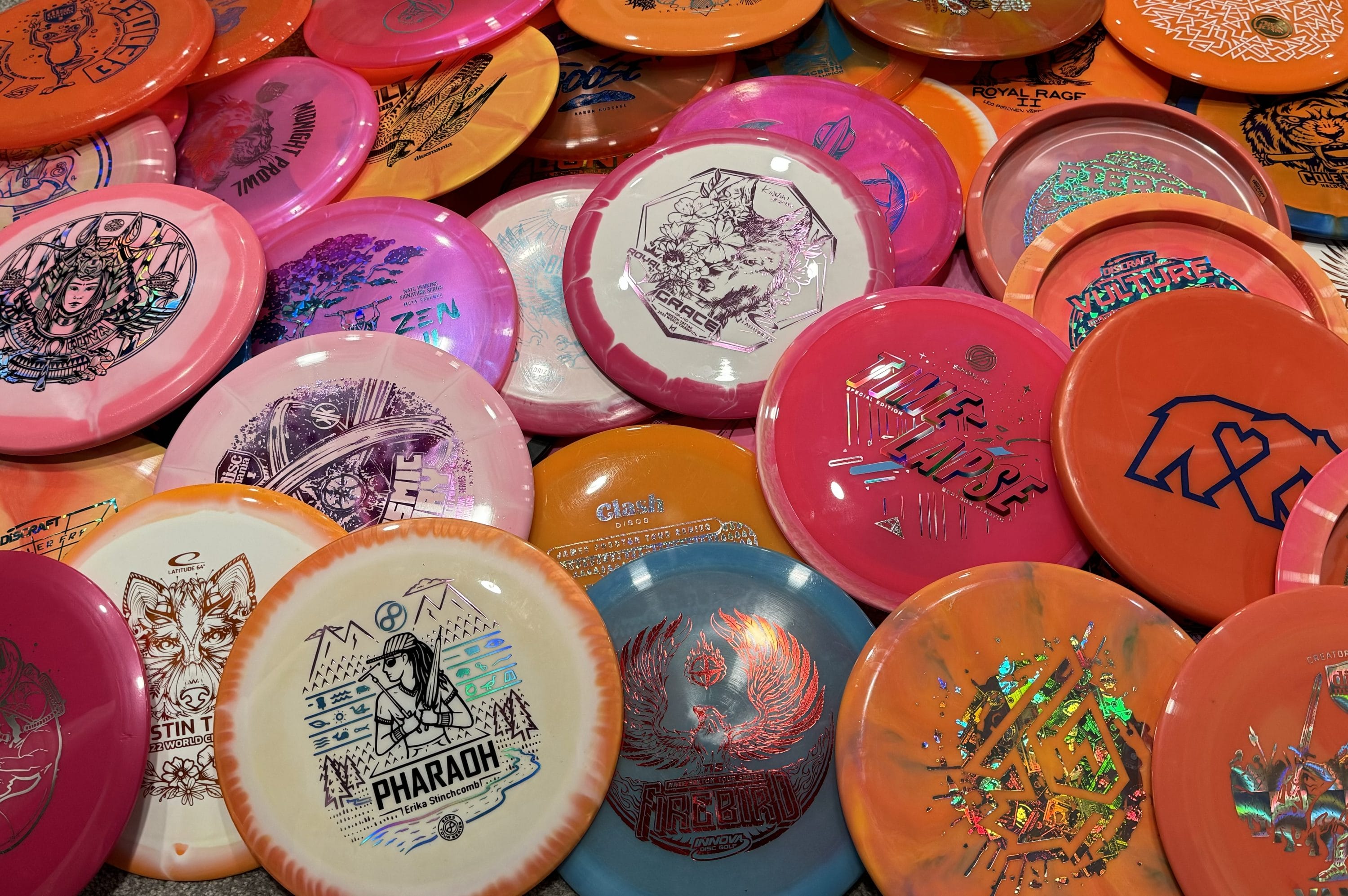
Disc Manufacturing: Confronting the Challenge of Inconsistency
In the intricate world of disc production, manufacturers face a persistent and complex challenge: inherent variability in the manufacturing process. Each disc created is subtly unique, presenting a nuanced problem that demands innovative solutions.
The root of this inconsistency lies in the multiple stages of disc production. From material selection to molding, pressing, and finishing, numerous variables can introduce slight deviations. Temperature fluctuations, material composition variations, and precision of equipment all contribute to creating discs that are never exactly identical.
Modern manufacturers are not simply accepting this variability as an unavoidable fate. Advanced quality control technologies, precision engineering, and statistical process control are being deployed to minimize these inconsistencies. Cutting-edge techniques like real-time monitoring, machine learning algorithms, and ultra-precise calibration are transforming how discs are manufactured.
While perfect uniformity might remain an elusive goal, the industry is making remarkable strides in reducing variability. By embracing technological innovation and rigorous quality management, manufacturers are progressively narrowing the gap between ideal consistency and practical production realities.
The journey towards more uniform disc production continues, driven by technological advancement and an unwavering commitment to quality.
Disc Manufacturing Mysteries: Unraveling the Precision Puzzle in Disc Production
In the intricate world of disc manufacturing, a complex challenge lurks beneath the surface of seemingly uniform production processes. Manufacturers and enthusiasts alike grapple with the subtle variations that emerge during disc creation, raising critical questions about consistency, quality control, and the fundamental limitations of current production techniques.Mastering the Art of Precision: When Manufacturing Meets Innovation
The Manufacturing Complexity Landscape
Modern disc production represents a sophisticated intersection of material science, engineering precision, and manufacturing technology. Each disc's creation involves multiple intricate steps where microscopic variations can dramatically impact performance. Raw material selection becomes a critical first stage, with polymers and composite materials requiring meticulous screening to ensure baseline consistency. Manufacturers must navigate complex chemical compositions, understanding how molecular structures influence disc characteristics like flexibility, durability, and aerodynamic properties. The manufacturing process itself introduces numerous potential deviation points. Temperature fluctuations during molding, pressure variations, and even subtle differences in mold design can generate imperceptible yet significant variations. Advanced manufacturers are increasingly employing statistical process control methodologies, utilizing sophisticated measurement technologies to track and minimize these variations.Technological Interventions in Production Consistency
Cutting-edge technological solutions are emerging to address manufacturing inconsistencies. Artificial intelligence and machine learning algorithms now analyze production data in real-time, identifying potential deviation patterns before they manifest in final products. Robotic systems with micron-level precision are replacing traditional manual processes, reducing human-induced variability. Specialized sensors embedded within production lines continuously monitor environmental conditions, material properties, and manufacturing parameters. These intelligent systems can instantaneously adjust production variables, creating a dynamic, self-correcting manufacturing environment. Thermal imaging technologies and advanced spectroscopic analysis provide unprecedented insights into material behavior during production.Material Science and Molecular Engineering
Revolutionary approaches in material science are transforming disc manufacturing paradigms. Researchers are developing smart polymers with adaptive molecular structures that can self-regulate during production. Nanotechnology enables precise manipulation of material properties at the molecular level, potentially creating discs with unprecedented consistency. Computational modeling now allows manufacturers to simulate entire production processes before physical implementation. These digital twins of manufacturing systems help identify potential variation sources, enabling proactive design modifications. By understanding complex interactions between material properties, environmental conditions, and production techniques, manufacturers can develop more robust and consistent production methodologies.Quality Control and Measurement Strategies
Sophisticated quality control mechanisms have become essential in modern disc manufacturing. Advanced metrology techniques, including laser scanning, coordinate measurement machines, and non-destructive testing methods, provide comprehensive assessments of disc characteristics. These technologies can detect variations as minute as micrometers, ensuring that each produced disc meets stringent performance standards. Statistical sampling techniques have evolved beyond traditional approaches. Machine learning algorithms now analyze comprehensive datasets, identifying nuanced patterns that human inspectors might overlook. This data-driven approach transforms quality control from a reactive to a predictive discipline, anticipating potential manufacturing variations before they impact product performance.Economic and Performance Implications
Manufacturing inconsistencies carry significant economic consequences. Variations in disc performance can translate to substantial competitive disadvantages in precision-driven industries like sports and professional applications. Each deviation represents not just a technical challenge but a potential economic liability. Manufacturers investing in advanced consistency technologies gain competitive advantages. By reducing variation, they can offer more reliable products, build stronger brand reputations, and potentially command premium pricing. The pursuit of manufacturing perfection becomes a strategic differentiator in increasingly sophisticated markets.RELATED NEWS
Companies
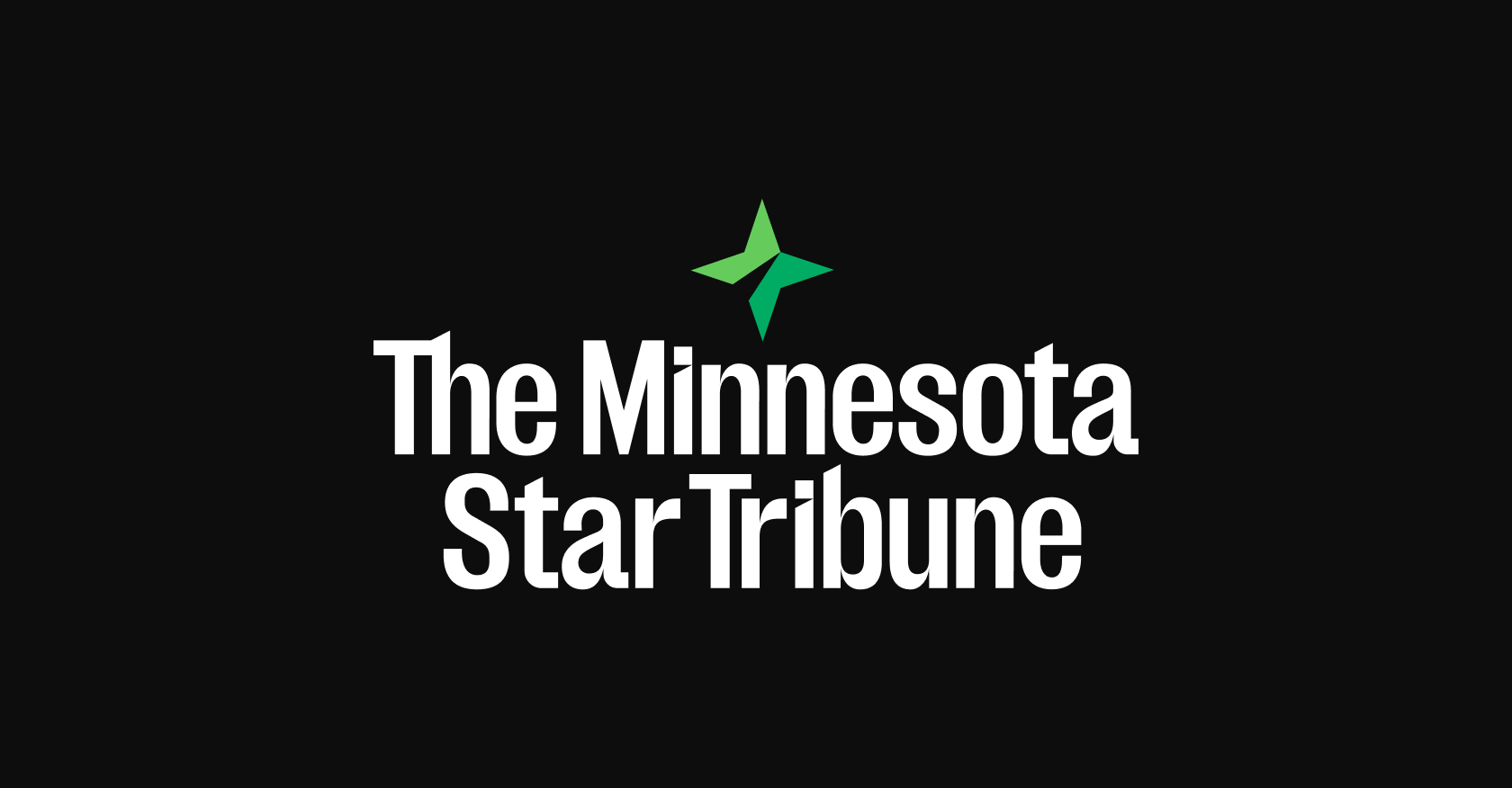
Climate Clash: Feds Challenge State Lawsuits Targeting Big Oil's Environmental Impact
2025-05-01 17:34:01
Companies
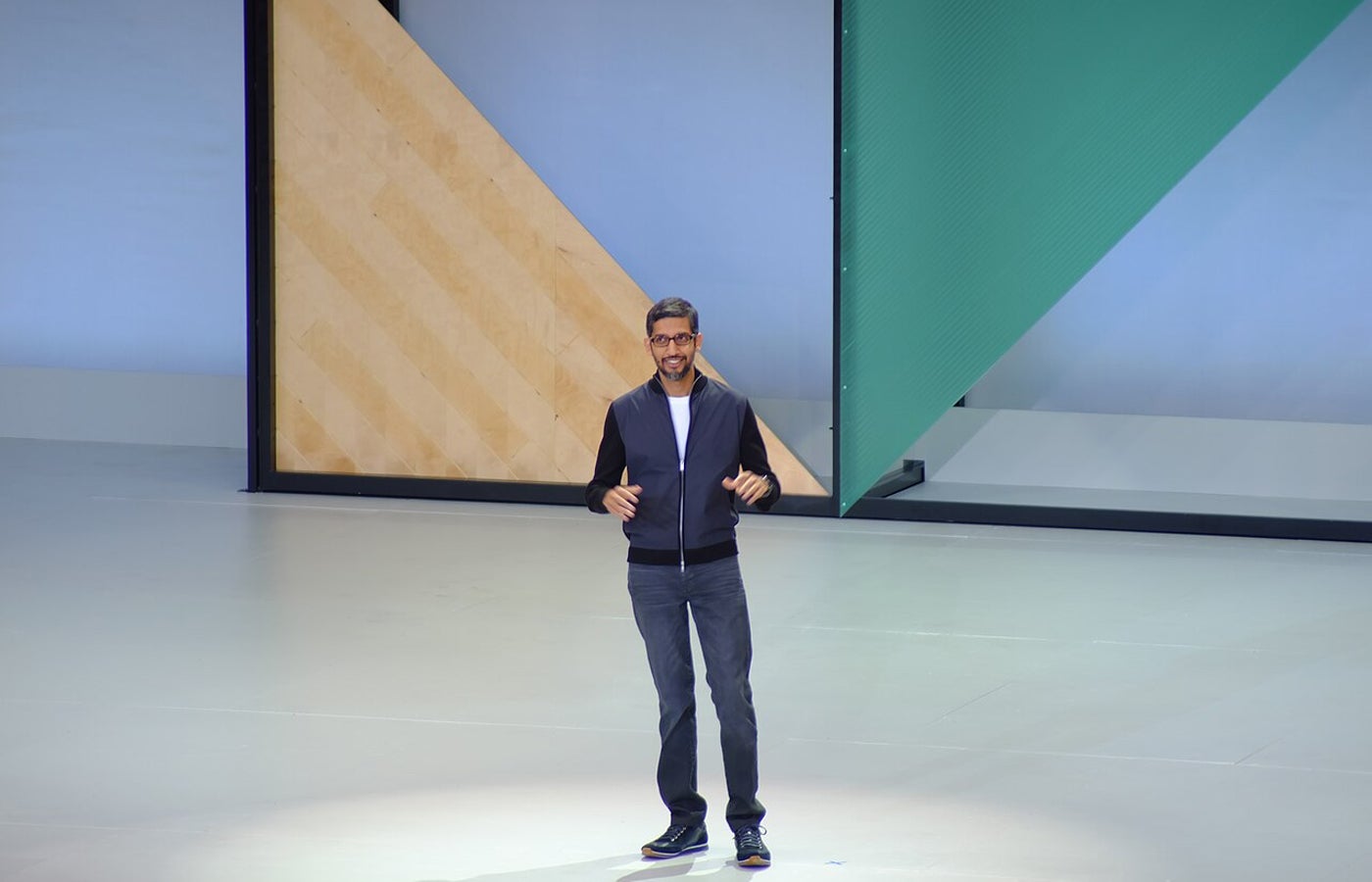
Climb the Corporate Ladder: 10 Powerhouse Companies Fueling American Career Dreams
2025-04-16 07:12:36